PCD Materials
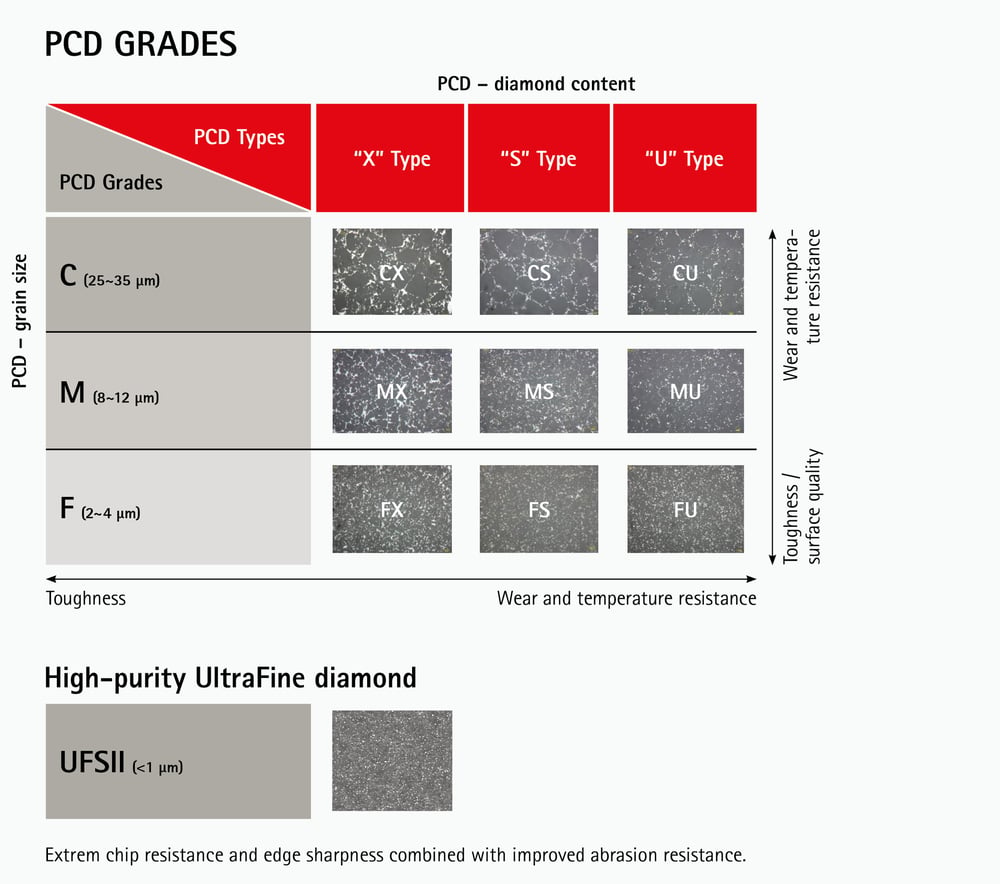
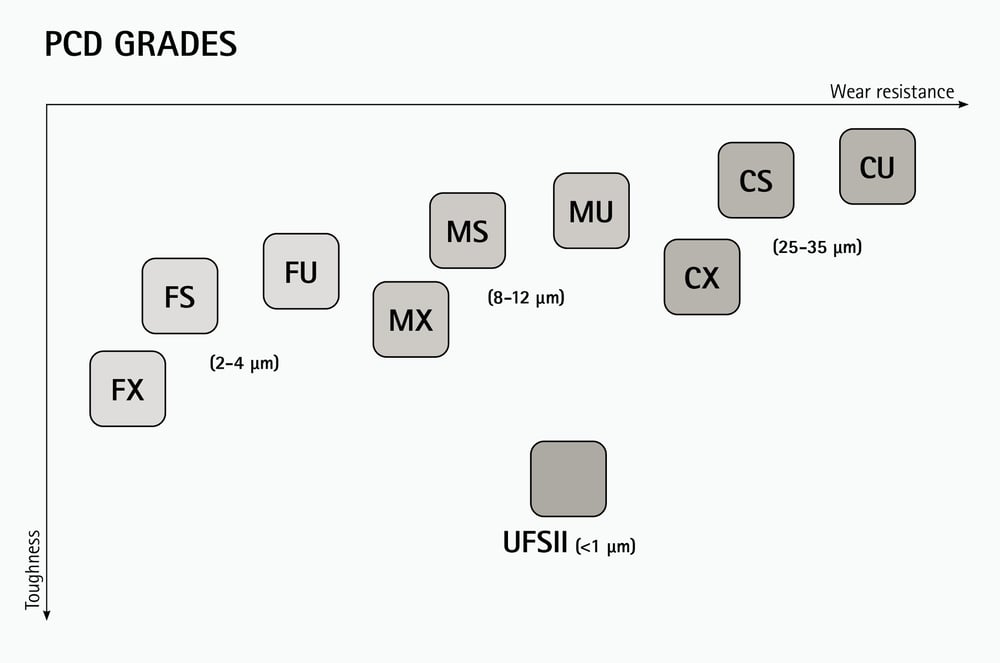
ADICO PCD is largely divided into coarse, medium and fine grades. By adjustment of the diamond and binder content ADICO developed 3 series (X, S, and U) to offer the perfect grade for your needs. The characteristics of each types are described in the table below.
Type | "X" series | "S" series | "U" series |
Microstructure and Characteristics |
Increased metal binder phase for high mechanical impact resistance. Little chipping and high grindability during production of PCD tools. Shows good electrical conductivity, performs with superior cutting speed during EDM processing. |
High diamond content, for excellent abrasion resistance due to high hardness. Reliable performance in a wide application area. Even fine finish can be achieved in high silicon aluminum. |
This series is characterized by a maximized diamond content and an advanced diamond to diamond bonding. Designed for highly abrasive applications and materials. |
ADICO PCD Cutting Tool Blank Application Areas
Fine grain PCD ("2-4 µm") | Finishing applications, wear parts, routers |
FX | Si-Al alloys, Plastics, Fiberglass |
FS | Si-Al alloys, Plastics, Fiberglass |
FU | Highest abrasion resistance in fine grain PCD area (ex. best surface finish for fuselage) |
UFSII (submicron) | Mirror finishing Al alloys. Composite machining, Titanium |
Medium grain PCD ("8-12 µm") | Finishing & Roughing applications - general Woodworking |
MX | Medium Si content Al alloys, Particle board, MDF, Cement board |
MS | Medium Si content Al alloys, abrasive plastics, abrasive wood-based boards |
MU | Difficult-to-machine material (carbon-fibre composite, CFRP, ceramic parts, Al2O3-coated laminated floor) |
Coarse grain PCD ("25-35 µm") | Wear related applications |
CX | High Si content Al alloys, Metal matrix composites (MMC), Plastic composites (glassfiber) cast iron (ex. crank-shaft bore machine) |
CS | High Si content Al alloys, MMC-milling, ceramics, WC-machining |
CU | Difficult-to-machine material (ex. carbon-fibre composite body, PCB, CFRP, SiC reinforced Al-alloys, Kevlar) |
* ADICO PCD Characteristics Chart
Disc dimensions
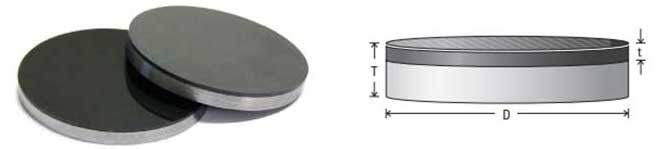
|
Sandwich PCD
Sandwich PCD is composed of PCD layer that is sandwiched by tungsten carbide layers in both(top & bottom) sides, primarily used for drilling application.
T: Blank thickness
t: Diamond layer thickness
Physical dimension
Half-moon of blank diameter: 62 mm
Blank thickness (T) | Diamond layer thickness (t) |
1.5 mm ±0.05 | 0.5 mm ±0.10 |
2.0 mm ±0.05 | 0.8 mm ±0.10 |
2.5 mm ±0.05 | 1.0 mm ±0.10 |
Product Offer : Blank Type (62 Ø & half-moon) Wire EDM Cut Type ( ,
per customer’s spec)
![]() |
![]() |
Laser Weldable PCD
An extra metal layer of PCD tungsten carbide substrate allows a new laser welding that brings lots of benefits over the conventional brazing for manufacturing PCD tipped blades.
Product Offer:
- Cut-pieces 3.2 mm (wire EDM cut)
- Exceptionally high bond strength at the welding joint between PCD and tool body.
- No risk of tool failure from unstable thermal stability related preblems.
- Cost effectiveness from no brazing.
- Offers both less health hazardous and cleaner environmental operation.
Application for Laser Welded PCD Tools:
- Saw blades for cutting tiles, rocks, cement boards.
- Saw blades for road grooving cement and asphalt.
- Core bits for drilling rocks, bricks, ceramics, etc.
- Others (like conventional PCD tools)